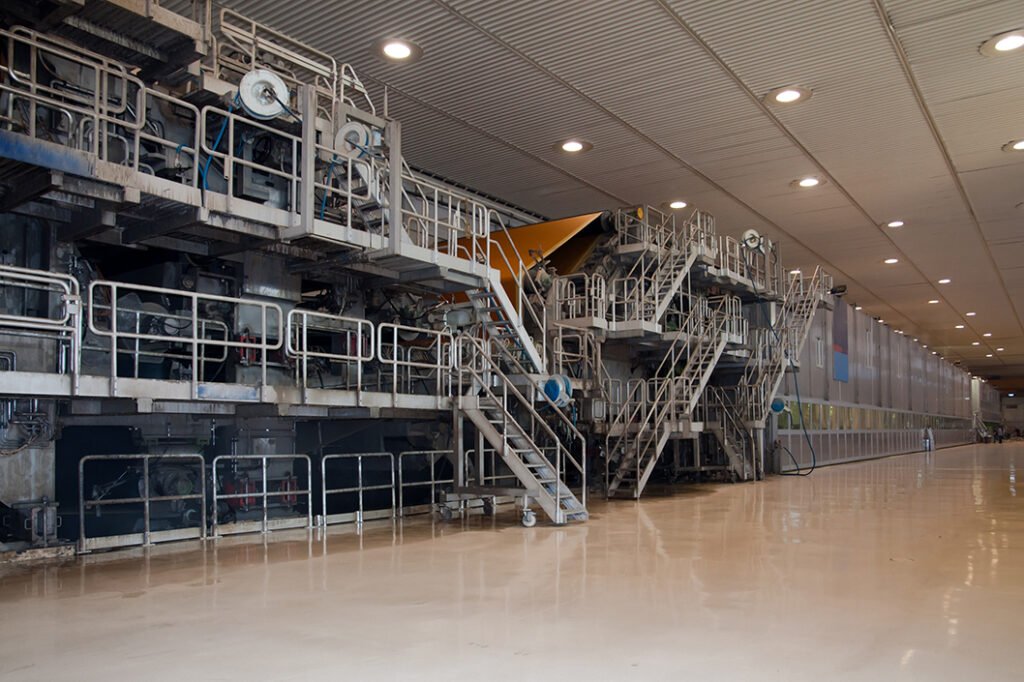
Background—A material of thousands of years of history
Formed from wood pulp or plant fiber, paper is chiefly used for written communication. The earliest paper was papyrus, made from reeds by the ancient Egyptians. The prototype of modern Paper was made by the Chinese in the second century, by a Chinese court official named Cai Lun. His paper was made from such things as tree bark and old fish netting. Recognized almost immediately as a valuable secret, it was 500 years before the Japanese acquired knowledge of the method. Papermaking was known in the Islamic world from the end of the eighth century A.D.
Knowledge of papermaking eventually moved westward, and the first European paper mill was built at Jativa, in the province of Valencia, Spain, in about 1150. By the end of the 15th century, paper mills existed in Italy, France, Germany, and England, and by the end of the 16th century, paper was being made throughout Europe.
Paper, whether produced in the modern factory or by the most careful, delicate hand methods, is made up of connected fibers. The fibers can come from a number of sources including cloth rags, cellulose fibers from plants, and, most notably, trees. The use of cloth in the process has always produced high-quality paper. Today, a large proportion of cotton and linen fibers in the mix create many excellent papers for special uses, from wedding invitation paper stock to special paper for pen and ink drawings.
Raw Materials-From mother nature
Probably half of the fiber used for paper today comes from wood that has been purposely harvested. The remaining material comes from wood fiber from sawmills, recycled newspaper, some vegetable matter, and recycled cloth. Coniferous trees, such as spruce and fir, used to be preferred for papermaking because the cellulose fibers in the pulp of these species are longer, therefore making for stronger paper. These trees are called “softwood” by the paper industry. Deciduous trees (leafy trees such as poplar and elm) are called “hardwood.” Because of increasing demand for paper, and improvements in pulp processing technology, almost any species of tree can now be harvested for paper.
Some plants other than trees are suitable for paper-making. In areas without significant forests, bamboo has been used for paper pulp, as has straw and sugarcane. Flax, hemp, and jute fibers are commonly used for textiles and rope making, but they can also be used for paper. Some high-grade cigarette paper is made from flax.
Cotton and linen rags are used in fine-grade papers such as letterhead and resume paper, and for banknotes and security certificates. The rags are usually cuttings and waste from textile and garment mills. The rags must be cut and cleaned, boiled, and beaten before they can be used by the paper mill.
Other materials used in paper manufacture include bleaches and dyes, fillers such as chalk, clay, or titanium oxide, and sizings such as rosin, gum, and starch.
The Manufacturing Process
Making pulp
• Several processes are commonly used to convert logs to wood pulp. In the mechanical process, logs are first tumbled in drums to remove the bark. The logs are then sent to grinders, which break the wood down into pulp by pressing it between huge revolving slabs. The pulp is filtered to remove foreign objects. In the chemical process, wood chips from de-barked logs are cooked in a chemical solution. This is done in huge vats called digesters. The chips are fed into the digester and then boiled at high pressure in a solution of sodium hydroxide and sodium sulfide. The chips dissolve into pulp in the solution. Next, the pulp is sent through filters. Bleach may be added at this stage or colorings. The pulp is sent to the paper plant.
Beating
• The pulp is next put through a pounding and squeezing process called, appropriately enough, beating. Inside a large tub, the pulp is subjected to the effect of machine beaters. At this point, various filler materials can be added such as chalks, clays, or chemicals such as titanium oxide. These additives will influence the opacity and other qualities of the final product. Sizings are also added at this point. Sizing affects the way the paper will react with various inks. Without any sizing at all, a paper will be too absorbent for most uses except as a desk blotter. A sizing such as starch makes the paper resistant to water-based ink (inks actually sit on top of a sheet of paper, rather than sinking in). A variety of sizings, generally rosins and gums, is available depending on the eventual use of the paper. Paper that will receive a printed design, such as gift wrapping, requires a particular formula of sizing that will make the paper accept the printing properly.
Pulp to paper
• In order to finally turn the pulp into paper, the pulp is fed or pumped into giant, automated machines. One common type is called the Fourdrinier machine, which was invented in England in 1807. The pulp is fed into the Fourdrinier machine on a moving belt of fine mesh screening. The pulp is squeezed through a series of rollers, while suction devices below the belt drain off water. If the paper is to receive a water-mark, a device called dandy moves across the sheet of pulp and presses a design into it.
The paper then moves onto the press section of the machine, where it is pressed between rollers of wool felt. The paper then passes over a series of steam-heated cylinders to remove the remaining water. A large machine may have from 40 to 70 drying cylinders.
Finishing
• Finally, the dried paper is wound onto large reels, where it will be further processed depending on its ultimate use. Paper is smoothed and compacted further by passing through metal rollers called calendars. A particular finish, whether soft and dull or hard and shiny, can be imparted by the calendars.
The paper may be further finished by passing through a vat of sizing material. It may also receive a coating, which is either brushed on or rolled on. Coating adds chemicals or pigments to the paper’s surface, supplementing the sizings and fillers from earlier in the process. Fine clay is often used as a coating. The paper may next be supercalendered, that is, run through extremely smooth calendar rollers, for a final time. Then the paper is cut to the desired size.
Read more: http://www.madehow.com/Volume-2/Paper.html#ixzz6dIFKopey